Ever since we announced our plans to introduce Mapvision Absolute Measurement, we have been getting a lot of questions about how the solution works in practise. This is natural, Mapvision Absolute Measurement changes quality inspection fundamentally, and those in the know will want to understand how we can go about measuring inline without a CMM (Coordinate Measuring Machine).
One of the most typical first questions has been about correlation. The correlation of measuring systems has traditionally been performed with a separate CMM, and now we are saying that with Mapvision Absolute Measurement, you don’t need a CMM at all. That sounds wonderful, but what do you do if the OEM still demands “correlation”?
Redefining Correlation of Inspection Systems
Correlation with a CMM does not create any value. It has just been the nature of relative measurements that has required this additional step, which from the process control point of view is simply a hindrance.
Luckily, this step can be completely avoided with the new systems. When in-line quality inspection goes absolute, the measuring system effectively becomes an inline CMM. Correlation in its old sense is no more needed, or even defined. It becomes a thing of the past.
Verifying the accuracy of inline measurement systems without a CMM
When the CMM is replaced by an inline quality inspection system with absolute measurement functionality, the system naturally needs to be calibrated and validated in a similar way as CMM’s have been before.
To solve this issue, Mapvision is introducing an easy-to-use shop floor artefact for checking Mapvision Quality Gate absolute accuracy as often as desired.
The Mapvision Absolute Measurement artefact follows the idea of the same VDI 2634-1 recommendation as the design phase artefact we use for internal testing before shipping the Mapvision Quality Gate system. The artefact is available with a calibration certificate from a DAkkS accredited measurement laboratory by default. It can also be calibrated elsewhere on demand.
System verification with Mapvision Absolute Measurement Artefact
To perform the system verification with Mapvision Absolute Measurement Artefact, the shop floor artefact is measured in one position inside Mapvision Quality Gate. This does not require any assembly or other special preparations.
Mapvision Absolute Measurement verification procedure results compared to DAkkS reference values.
The artefact contains seven independent bars with targets, and the distances between the targets are known accurately from the calibration certificate. As the whole artefact is fixed and the bars are multi-faceted, the whole verification process can be carried out in one position and one measurement cycle in about 20 seconds.
Mapvision Absolute Measurement together with the shop floor artefact is a factory-CMM-independent, traceable and absolute inline measuring solution that delivers the ultimate promise of inline: You can now measure and adjust your production in real-time without a CMM!
For more about Mapvision Absolute Measurement and links to the previous posts in this blog series, please visit our Mapvision Absolute Measurement solution page.
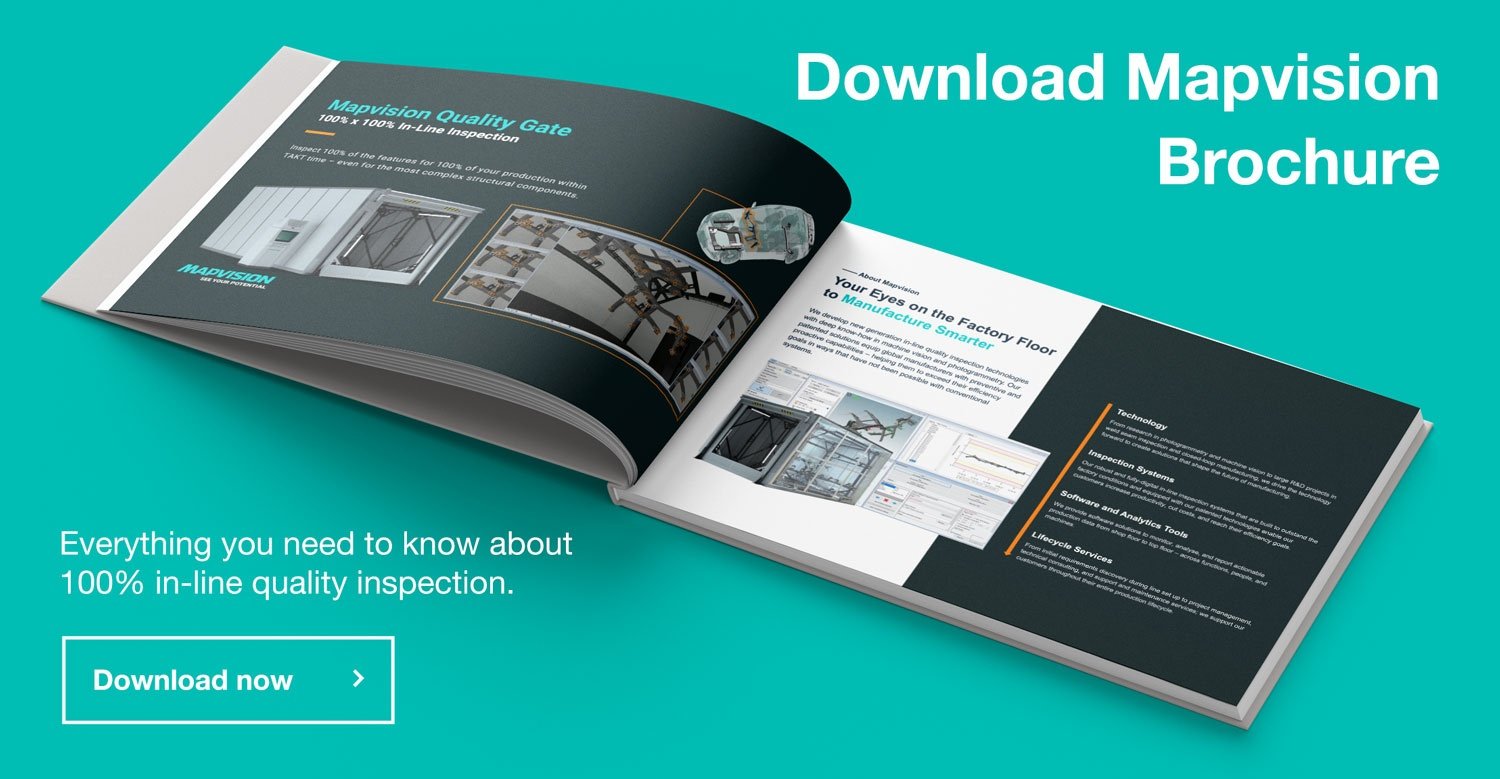
PUBLISHED BY
Kosti Kannas
Kosti Kannas is in charge of product development as CTO. He has over 10 years of experience developing and delivering for the automotive industry. With his roots in automation technology and sustainability topics, he is set to disrupt the manufacturing world with new levels of flexibility and agility in in-line measuring. Interested in all things related to tying the simulated and the real world together.