The laboratory for additive manufacturing (LaF) at Landshut University, deals with the process of reverse engineering headed by Prof. Dr.-Ing. Norbert Babel. This includes scanning objects, scanning data processing using special software tools and transfer to a CAD system, modeling and simulating, as well as generating prototypes developed which are manufactured with different additive manufacturing processes. This takes place across faculties in research projects, along with student’s project, bachelor and master thesis.
Since there is an increasing demand on patient-specific individualization in medicine, primarily in the field of prosthetics, students on the Biomedical Engineering course were assigned to develop individualized finger splint orthosis.
As a first step, the students scanned a hand with Creaform Go!SCAN 3D scanner for which the orthosis should be developed (fig. 1). Then, data has been treated in VXelements software (fig. 2). This means cleaning up the overlapping image points and removing geometry offsets. The reduced scan file will be stored in STL format for further processing with Rapidform program (fig. 3).

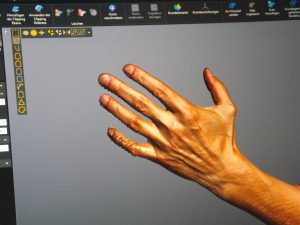
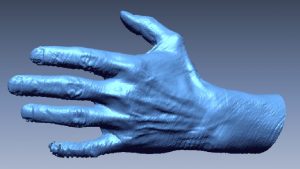
Rapidform, from the company 3D-Systems, is a software package that combines 3D scan data processing and parametric volume modeling, in order to create intelligent CAD models from point clouds and polygon meshes [1]. This means that “watertight” STL models can be created, which is the requirement for the conversion of triangulated STL networks into a structure of NURBS surfaces (fig. 4), from which then, ultimately, volume modules of the software can be generated.
These volume data are imported via the standardized IGES interface from and into a CAD system (here CREO of version 4.0). The purpose of the implementating Boolean operations with the scanned data and the orthosis geometry is already created in CAD for the areas of individual adaptation. Finally, the CAD data was produced, installed and tested using additive manufacturing processes (fig. 5).
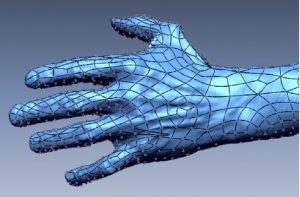
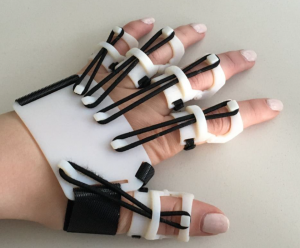
Our experience with Go!SCAN 3D is very positive. We were particularly inspired by scan data processing within Vxelements software. This represents the decisive interface between the scanner and the scanned object, which is brilliantly achieved here, as the entire scan process is crucially dependent on the functionality, handling and performance of the scanner software.
Performing scans are very fast and immediately visible and adjustable on the screen by the quasi “real-time display” of the scanned geometry, which ensures the good results in terms of quality that can be produced.
The light, intuitive operation with numerous tutorial and training videos, ensures that the handling of both, the scanner and the software, is easy to learn and can be integrated easily into student projects.
[1] 3D-Systems website
https://www.3dsystems.com/press-releases/rapidform-xor-3d-scanning-software-receives-good-software-certification
ARTICLE WRITTEN BY Creaform
Prof. Dr.-Ing. Norbert Babel, HaW Landshut
Really informative blog article. Really thank you! Want more. Ashleigh Galvin Kluge