As a company that handles all processes from producing high-precision wooden and foam molds to casting and machining, KISHIMOTO IRON WORKS faced a pressing need to improve casting inspection efficiency. By introducing the FreeScan UE Pro and Geomagic Control X, the company increased casting inspection efficiency by 300%, eliminating delivery delays.
Information
Company Name: KISHIMOTO IRON WORKS
Location: Japan
Need: Improve casting inspection efficiency
Solution: FreeScan UE Pro, Geomagic Control X
Result: Casting inspection efficiency has increased by 300%, and delivery time is no longer delayed.
About KISHIMOTO IRON WORKS
KISHIMOTO IRON WORKS is located in Tsuyama City, Okayama Prefecture. The company manufactures gas valves, agricultural equipment, and industrial machinery parts by casting FC (flake graphite cast iron) and FCD (spheroidal graphite cast iron). The company’s strength lies in its ability to handle all processes, from producing high-precision wooden and foam molds to casting and machining.
Image from left: Junichi Isoyama, General Manager of Ironworks Department / Tatsuro Hirai, Director and Factory Manager / Kohei Kishimoto, General Manager of Casting Department
Background
In recent years, casting manufacturers have increasingly requested detailed evidence of quality control. Inspecting the finished product to see if it matches the design is essential. KISHIMOTO IRON WORKS introduced a 3D coordinate measuring machine about 15 years ago and has been working on quality control ever since. Although 3D measuring machines are accurate and can prevent human error, measuring each product takes 4 to 6 hours.
“We measure castings twice: first at the ‘raw material’ stage after processing the sprue, and again at the ‘post-processing’ stage after machining tasks like drilling, chipping, and flattening. Doing both with one machine creates congestion in the inspection process, overburdens staff, and causes delivery delays,” explained Mr. Hirai.
Start Casting Inspection with 3D Scanners
KISHIMOTO IRON WORKS has been interested in 3D scanners for some time. After displaying several demos, they chose SHINING 3D FreeScan UE Pro. FreeScan UE Pro has an extremely high cost-performance ratio compared to other companies’ products, and the cost makes it easy to introduce. The accuracy requirement for castings in the “material” stage is about 0.1 mm, which FreeScan UE Pro easily achieves. They were surprised at how accurate the measurements were and how quickly they could be completed in just one-quarter the time it normally would. The scanner and the accompanying software are both easy to operate and understand.
How does KISHIMOTO IRON WORKS use FreeScan UE Pro for Casting Inspection?
Using the FreeScan UE Pro, KISHIMOTO IRON WORKS scanned the castings they manufactured. By carefully putting markers, they quickly and accurately scanned even the complex shapes of the castings down to the finest details.
The scanned data is then imported into Geomagic Control X 3D inspection software to check for manufacturing errors. The inspection process time has now reduced from 4-6 hours to about 1 hour, preventing delivery delays even during busy production periods.
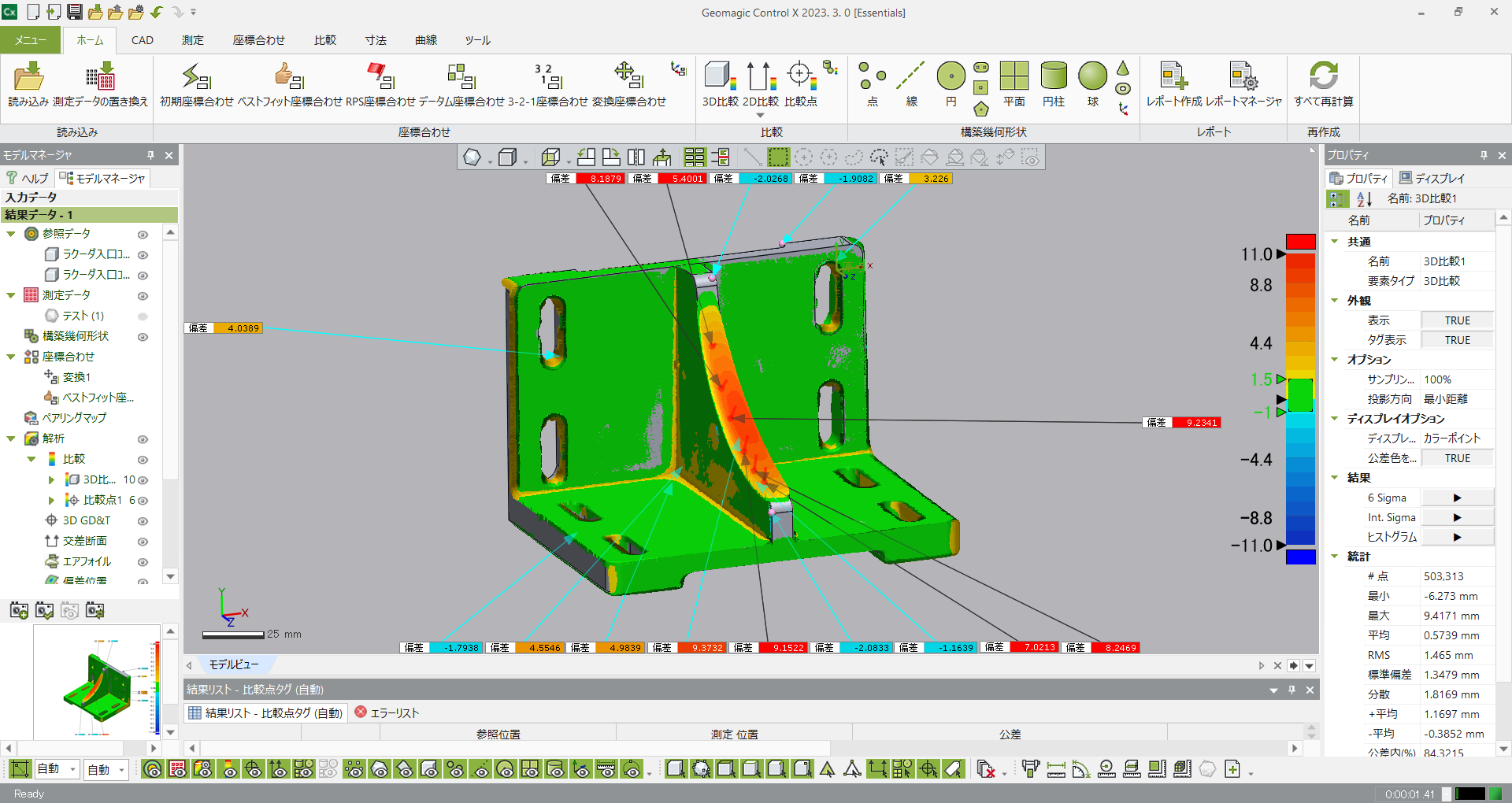
Feelings about Using 3D Scanning Technology
“We realized that the 3D scanner perfectly fits the casting industry in terms of accuracy, speed, and cost,” said Mr. Hirai. “As a company providing a one-stop service from wooden molds to casting and processing, we see potential to expand the use of 3D scanners to include the manufacturing process of the wooden molds themselves, as well as in reverse engineering, where we take measurements of actual items and create 3D drawings.”