CAD translation validation became an industry-wide requirement for commercial aircraft subcontract manufacturing via the Boeing DPD (digital product definition) D6-51991 standard. While translation validation software applications have other benefits and uses, the need for this quality control requirement remains mostly driven by the need for safety of flight for passenger carrying aircraft.
What is the Boeing D6-51991 standard?
The Boeing D6-51991 document is titled “Quality Assurance Standard For Digital Product Definition at Boeing Suppliers.” The latest revision N release, dated April 19, 2019, consolidates and replaces multiple Boeing requirements. The article outlines uniform specifications for supplier control of digital product definition data and specific requirements for CAD translation validation in section 8 and Product Acceptance Software (PAS) in section 3. This article will explore these two sections in greater detail.
Why validate CAD model translation?
Boeing and other aerospace manufacturers have stringent quality and safety requirements due to the critical nature of the components and systems used in aircraft. Inaccurate CAD model translations are a real issue and why Section 8 of D6-51991 exists. Here is a summary of why validation of CAD model translation is crucial in the manufacturing process.
- Safety and Regulatory Compliance: Aerospace products like commercial aircraft are subject to strict safety regulations. Any deviation from the original design, even minor ones in component dimensions or shape, can impact the safety and performance of the aircraft. To ensure compliance with these regulations, suppliers must validate CAD model translations to verify that the components they manufacture will meet the required specifications.
- Consistency and Quality Control: CAD models are the authority for designing and manufacturing aerospace components. CAD models must be translated accurately to maintain consistency and quality in manufacturing. Any errors or discrepancies in translation can lead to defects, inconsistencies, and quality issues in the final product.
- Fit, Form, and Function: The fit, form, and function of aerospace components are critical to success. Even minor differences in dimensions or shape can affect how parts fit together, potentially leading to assembly issues, reduced structural integrity, or operational problems. Validating CAD model translations helps ensure components fit together correctly and perform as intended.
- Traceability: In the aerospace industry, it’s crucial to have traceability and documentation throughout the supply chain. By validating CAD model translations, suppliers can provide evidence that the components they deliver are manufactured according to the specified design, which is essential for traceability and quality assurance.
- Risk Mitigation: For aerospace manufacturers, the cost of failures or quality issues can be substantial in terms of financial losses and safety risks. Validating CAD model translations is a proactive measure to mitigate these risks and prevent costly rework or safety-related incidents. To achieve these goals, Boeing and its suppliers employ Verisurf Validate software to verify CAD model translations are accurate and that the manufactured parts meet GD&T specifications. These processes help maintain the highest safety, quality, and precision required in the aerospace industry.
How CAD model translation validation works
Verisurf VALIDATE
CAD Model Validation for DPD Compliance
1 VALIDATE is also an excellent tool for configuration control, model-vs-model comparison
The Verisurf VALIDATE software application analyzes and verifies imported source, “authority” CAD models for Verisurf inspection. It provides comparison of the imported, “derivative” model to the original, native CAD source model, identifying any potential errors or distortions that might occur in the file translation process. The Verisurf VALIDATE optional product module includes fully integrated KUBOTEK KOSMOS Validate software and now comes included with the stand-alone version as well.
Verisurf is compatible with all native CAD model varieties.*
- Translator add-on required for some file formats
- Verisurf is compatible with most 3D metrology devices.
Verisurf-Embedded VALIDATE Workflow
Kubotek Kosmos VALIDATE – External Stand-Alone App
Verisurf VALIDATE’s original integrated software module performs validation on a CAD model after importing it into Verisurf using embedded Kubotek Kosmos functionality. Subsequently, Verisurf VALIDATE now includes the Kubotek Kosmos VALIDATE external, stand-alone application in addition to the integrated version.
With Kubotek Kosmos VALIDATE stand-alone, users import the “authority” or source CAD model into the application. In the stand-alone app, a “derivative” model in neutral file format such as IGES or STEP is also imported for comparison against the authority model. Kubotek Kosmos VALIDATE provides numerous comparison, analysis, display, and reporting features to comply with DPD. It also includes additional capabilities for configuration control among other benefits.
Advanced Geometric Comparison identifies, highlights and documents missing or inaccurate model geometry that would be hard or impossible to find with visual inspection.
Revision Change Management helps OEM configuration management communicate specific changes from one configuration to the next. In this case the slot width for part number 1234-5678 has been widened from 15.000 in configuration C to 15.200 in configuration D.
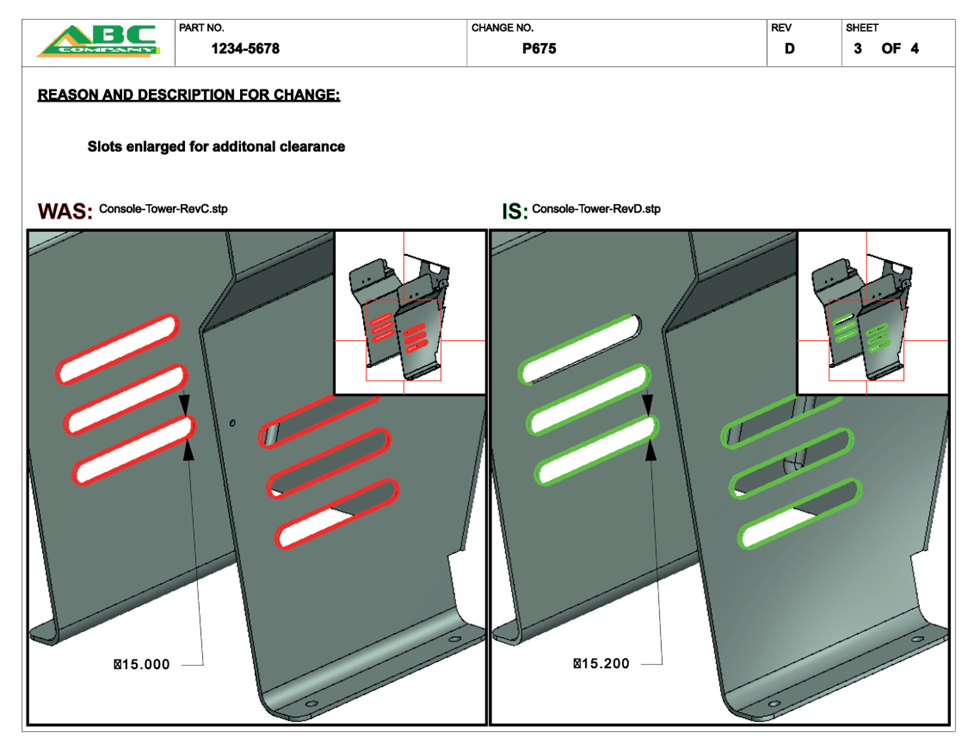
Geometry Orientation Validation identifies, highlights and documents differences in geometry orientation which often results from moving or rotating a part in an assembly or changes in part coordinate systems.
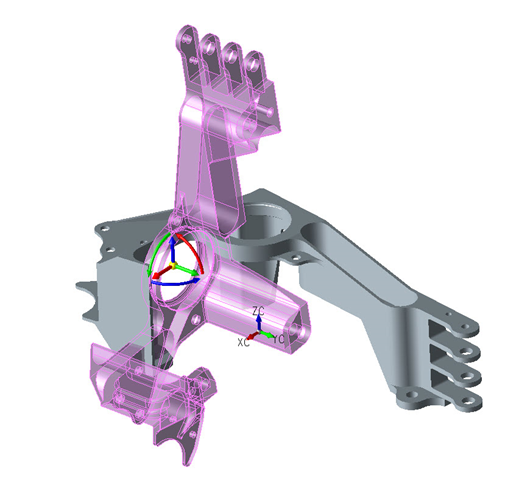
MBD Annotation Validation checks for differences in semantic GD&T that may occur during translation including small deviations in feature control frames which are very difficult to visually identify in complex parts. In this case the STEP AP242 model annotations matched but the NIST characters highlighted in red failed translation validation.
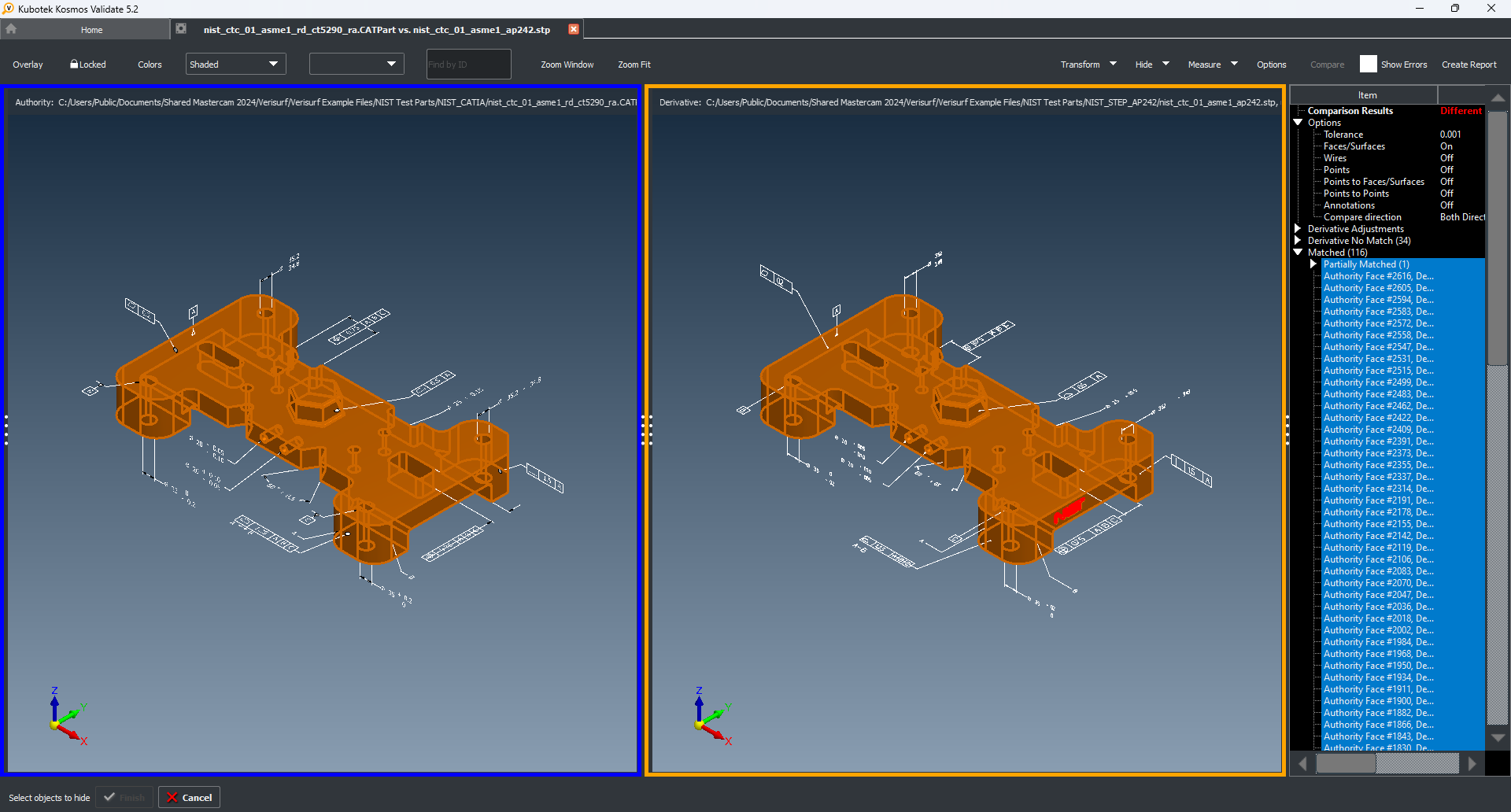
Validation Reports are an important part of the documentation process. In this case the differences between the Authority File and Derivative File are clearly listed in the software dialog, highlighted in the software graphics display and reported in a multipage sharable PDF file.
Kubotek Kosmos VALIDATE Workflow