This content was originally written and published by the Artec 3D team on their website. Reproduced here from this link.
It’s not every day that an engineering company gets to help a pet in need, but in one special case, the two worlds collided and a dog named Mimi was given a new lease on life with some of the newest technology available, Artec Space Spider.
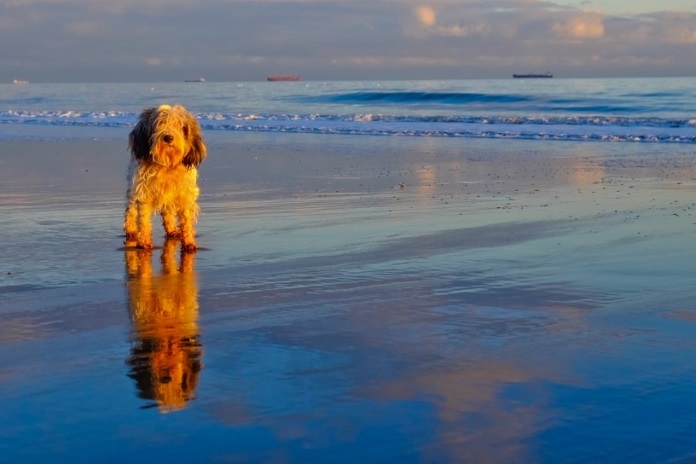
Adaptive Engineering Solutions Ltd. (AES), an engineering company in Newport, UK, has been using Artec Eva and Artec Space Spider handheld 3D scanners since 2015, chosen after visiting Artec 3D Gold Certified partner Patrick Thorn & Co. for a demonstration.
“The thing that clinched it for us was the option of scanning without putting dots all over the subject – which we saw as a massive inconvenience! We have used the scanners for a variety of tasks, from build inspections of wind turbine blades, reverse engineering of classic cars and boat hulls at one end of the spectrum, to quality inspections of miniature castings and injection-molded parts,” said Managing Director Gordon Mucklow.
But despite their large scanning portfolio, a very different and special project would soon come their way. Mimi first came into the picture when her owner, Ben, called them, desperate for someone to help. Born with a heart murmur and an overbite, Mimi’s struggle only increased after an attack by another dog when she was just five months old. This led to a punctured windpipe, an infection, and two throat operations. She was given a slim 10 percent chance of survival.
The vets acted quickly, doing all within their power to save her. Every measure was taken to ensure that Mimi would have a long and comfortable life ahead: a six-centimeter-long hole made in Mimi’s neck was fitted with a tube, allowing her to breathe. This tube requires cleaning three or four times a day and brings with it a constant fear that she may pick up an infection or suffocate due to blockage.
And then one day, the tube broke. Temporarily repaired with glue, time was of the essence and Mimi’s life depended on a quick solution. Ben needed to get hold of a tube that worked, and he needed to have spare tubes on hand for the next such emergency.
Desperate for help, Ben called local design companies seeking assistance but equipped with 3D printers rather than scanners, they had to turn the job down. As a dog-friendly company with a possible solution, the AES team knew they had to help. “We’re a K9 friendly office, so it was a real heart-jerker for us. We decided to help, as we could shuffle our workload around and were able to offer help and advice regarding the printing,” said Gordon.
Having worked with Gordon for years, Patrick Thorn has assisted AES in finding 3D scanning solutions across a number of projects. “Every now and then Gordon calls with a ‘how could I do this’ chat,” said Patrick. “This has resulted in all sorts of projects for them. This knowledge in turn led them to a crucial step: Finding a solution to help Mimi when no others could see a way forward.”
While confident they could find a solution, the job presented a number of challenges. “The part we were given to scan was a transparent medical grade plastic, but it had become embrittled over time and had already been repaired several times after a number of breakages,” explained Gordon. “Being engineers, we were keen to maintain the design intent of the original part – such as the internal tube cross-sections (to allow at least the same amount of airflow to pass through the tube), and to ensure that the ‘form’ of the new part was as close to that of the one we were provided with as possible, as it was the most comfortable for Mimi to use since she had rejected other tubes in the past.”
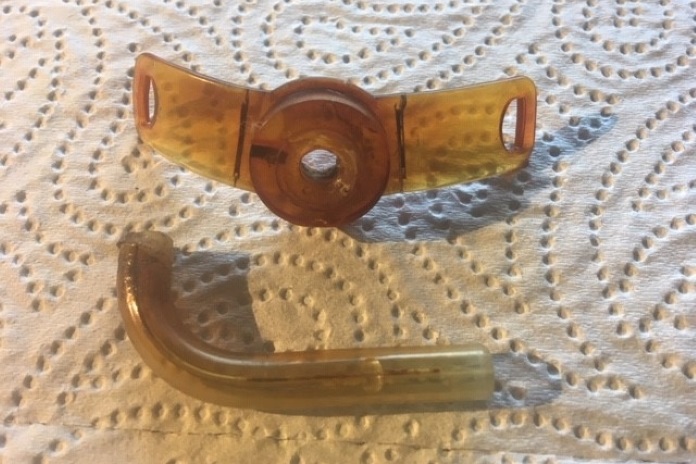
As a solution, the team used a soluble chalk spray to render the surface opaque, to enable them to perform the scan. Initial surfaces from the part were ready in about 30 minutes using Artec Studio 14 and Artec Space Spider. Two scans of the part came from different orientations on a turntable, which was then registered and aligned using tools within AS14. “A fast fusion was sufficiently accurate for the purposes of the geometry capture,” recalled Gordon, “all while being watched by a very anxious Ben!”
A high-resolution 3D scanner based on blue-light technology, Artec Space Spider is ideal for capturing small objects, or intricate details of large objects. The ability to render complex geometry including sharp edges and thin ribs, combined with high accuracy, makes it a leader in industrial scanning for capturing everything from molding parts to coins, keys to breathing tubes.
Adding Rhino software and Mesh2Surface to their process to allow modifications and alterations, Gordon and his team were able to create native CAD surfaces which they could then manipulate to recreate the part, remove any anomalies (on the scan of the actual broken part), and ensure that it was suitable for 3D printing.
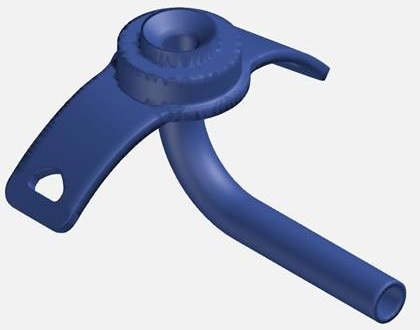
“We did all this within 24 hours of the first call and had sent the file to a 3D printing provider whom Ben had already spoken to, and they got the parts underway quickly,” said Gordon. “We’re absolutely pleased with the result. Without scanning, it would have taken huge amounts of time and effort to map the geometry by hand – as it was so unique to Mimi, it was important to keep some of the curvatures and dimensions as close to the original ones as possible. This really was an ideal project for the Artec Space Spider.”
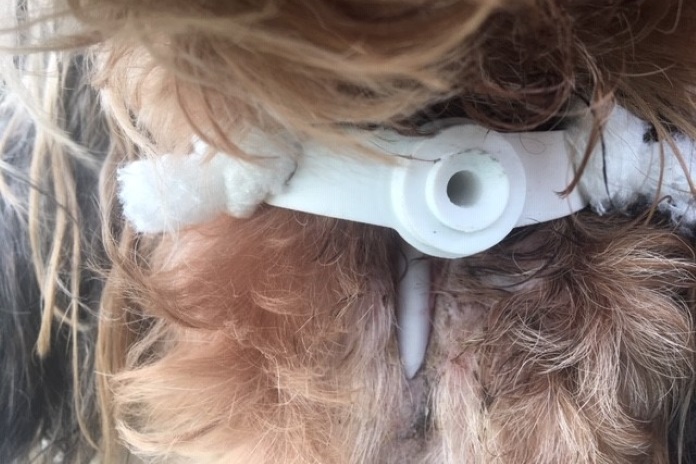
“It is indeed refreshing to meet a business that goes out of its way to help its customers,” said Ben, who is now working on an inspirational book about Mimi’s adventures. “Mimi and I are extremely grateful for their assistance, and I do not hesitate to recommend their services.”
AES is also glad to have been able to contribute to a project that’s a bit more personal – something rare for the engineering company. “The Mimi project was great to be involved with, and highlights our ability to diversify between huge, long-term engineering projects,” said Gordon, “and smaller, more immediate high-impact activities like helping Mimi breathe!”
To know more, please check Artec 3D.