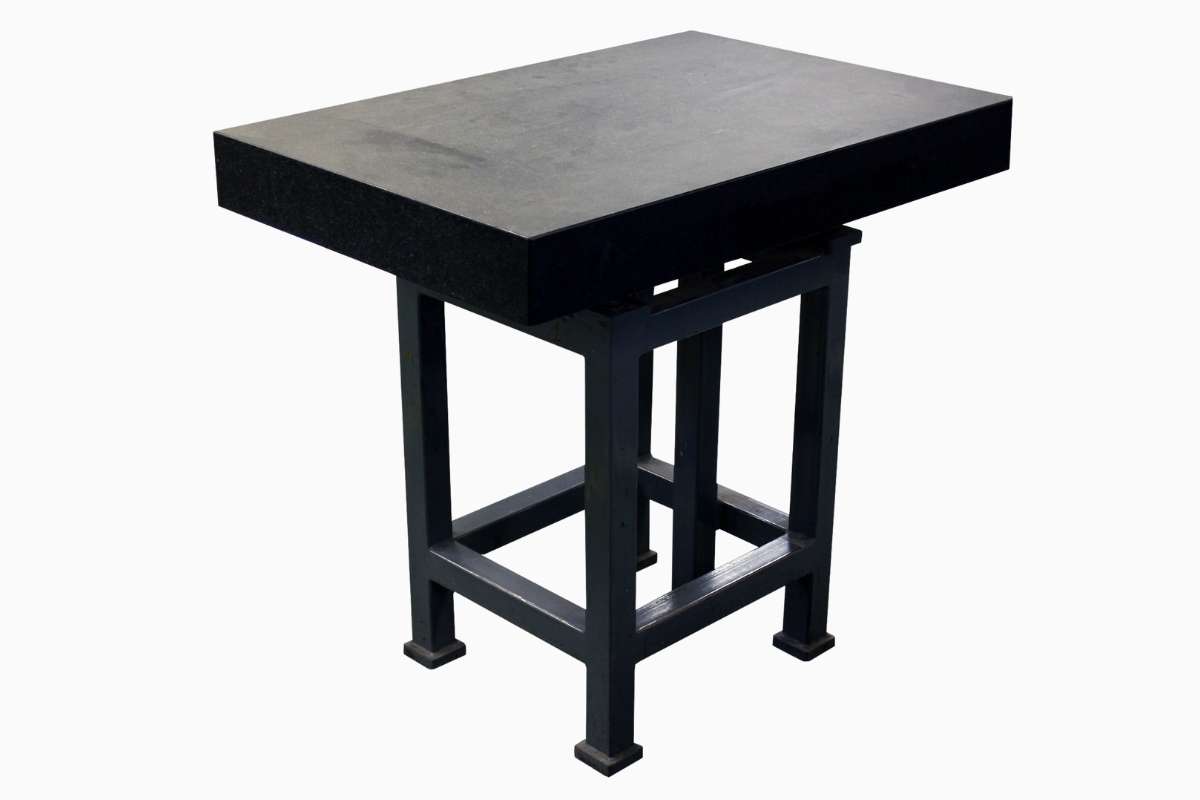
Manufacturing and engineering industries rely on accurate measurements to create reliable readings and safe products. In high stakes, high-quality business, granite surface plate calibration forms the core of responsible measurement maintenance. Appreciating the granite surface plate’s value in the workshop keeps operations efficient and cost-effective. With a mixture of formal and behavioural approaches to granite surface plate calibration and maintenance, workshops optimise their equipment from the ground up.
The Role of Surface Plates
Surface plates create a flat, engineered plane upon which to conduct measurements. Providing a robust and level surface, they eliminate variables to facilitate scientific accuracy. Granite surface plates often come with rubber pads on their underside to protect the surfaces beneath them and protect the stone itself. While, historically, workshop operators used various materials to create their surface plates, granite currently leads the market. This popularity stems from granite’s natural physical properties, which offer advantages in reliable measurements.
How Granite Shapes Surface Plates
Granite surface plates achieved mainstream popularity during the second world war, as military requirements made metal scarce. Engineers have turned to granite for its non-corroding, non-permeable, durable qualities ever since.
The stone’s natural rigidity and warp resistance creates effective and reliable surface plates. Granite’s igneous formation creates large, strong slabs of stone, rich with tightly-grained feldspar and quartz. This strength makes granite an excellent fit for construction and engineering projects all over the world. However, like any material, granite is not invincible. Granite surface plates, therefore, require calibration to maintain their efficacy and make the most of their desirable qualities.
What is Granite Surface Plate Calibration?
Surface plates change over time. The more workshops use granite surface plates, the more they change with wear and tear. Granite surface plate calibration works to manage and reverse these changes to keep surfaces level and readings accurate.
Calibration work falls into two categories: maintenance and formal calibration. All granite surface plate users should implement maintenance procedures to keep their equipment working accurately for as long as possible. However, workshops should also implement formal granite surface plate recalibration at least once a year to safeguard the quality of their output.
Regularly scheduled specialist granite surface calibration proves a workshops dedication to accuracy and helps pre-empt emergencies.
How Do Specialists Conduct Surface Plate Calibration?
Specialisation fuels industry and granite surface plate specialists service the stone with expertise and excellence. Technicians identify and solve faults and imperfections, hand-lapping plate surfaces back to purchase-point quality.
Depending on the size of the plate and the workshop’s requirements, calibration specialists can service plates on location or at their own premises. After calibrating, technicians also clean and coat the granite surface, a useful practice applicable all year round.
Granite surface plate calibration minimises disruption to businesses and maximises production quality.
How to Maintain Granite Surface Plate Calibration
Between formal calibrations, workshop behaviour practices also affect granite surface plates. These maintenance practices help make the most of each calibration and preserve the surface plate’s lifespan.
Only Use a Granite Surface Plate for Measurement
Many homes use granite surfaces for kitchens or bathrooms. Similarly, some workshops use granite surface plates for storage or resting food and drinks despite their metrological purposes.
When a granite surface plate becomes a coaster or a bench, it suffers from wearing and staining. Incorrect measurements and products stem from worn surfaces, and stains foster contamination. Granite surface plates should therefore be covered when not in use to preserve their calibration and uphold measurement quality.
Use Different Parts of the Granite Surface Plate
Workshops pay for the whole surface plate, so it makes sense to use every inch. Over-using the same place on a granite surface plate also increases wear and tear.
Operators make the most of their equipment by regularly changing the workpiece location and maintaining granite surface plate calibration. Of course, lifting and rotating the plate each time proves impractical. The weight of surface plates presents a risk to operators and the plate itself if dropped. Therefore, practical and well-equipped workshops rotate the table underneath the plate or use specialised apparatus to lift the plate safely.
Avoid Overloads or Scratches
Measured workpieces may feature rough or jagged edges. While machinists choose granite for its durability, regular contact with such edges may lead to chips or scratches.
Granite surface plate calibration and maintenance means minimising impacts and spreading loads over wide areas, not points. Resting flat edges on the surface plate protects the material while stabilising the workpiece. Spreading the load maintains surface plate calibration and keeps workplaces safe and effective.
Conclusions: The Advantages of Granite Surface Plate Calibration
Ultimately, surface plates are vital tools in every workplace and require just as much care, maintenance, and calibration as all the other equipment. Regular granite surface plate calibration builds the foundations for a reliable, high-quality workflow and a forward-thinking workshop.