Accuracy Assurance
SHINING 3D’s OptimScan 5M Plus provides core technical support for this automated inspection system. OptimScan 5M Plus has an accuracy of 0.005 mm and a point distance of 0.04 mm. It can easily capture complete data of complex details like tiny holes and deep grooves.
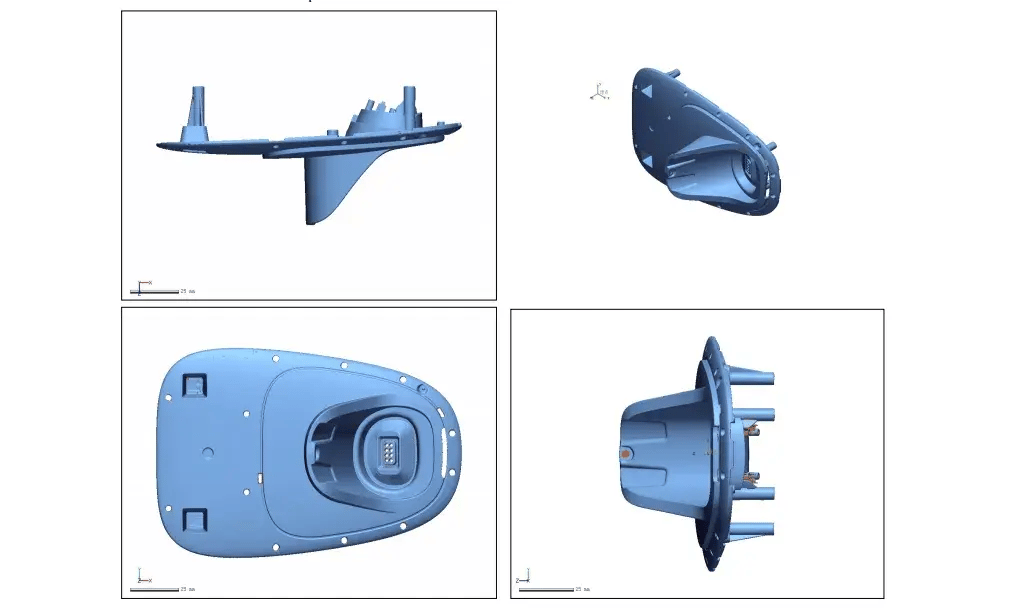
Data Traceability
The high-accuracy data obtained through 3D scanning lays the foundation for building a fully digital inspection system. Throughout the entire production chain—from mold design and mass production of parts to finished product inspection—the data from 3D scanning can be seamlessly imported into the company’s quality management information system. This achieves traceable quality records.
Conclusion
SHINING 3D’s automated inspection system offers a powerful solution for modern manufacturers facing increasing inspection challenges. By combining high-accuracy scanning, automation, and data traceability, this system not only ensures that incoming materials meet the highest standards but also significantly improves production efficiency. As manufacturing continues to evolve, adopting advanced technologies like this will be crucial for maintaining quality and staying competitive in a rapidly changing industry.