Filtration and flow control systems often require components with unique design geometries, intended to reduce pressure drop and energy consumption during use, that can be difficult, if not impossible to produce using traditional fabrication techniques. To help enable new capabilities for fabrication of filtration and flow control components, global engineering technologies company, Renishaw, supplied its new RenAM 500S Flex machine to Mott Corporation.
Mott Corporation based in Connecticut, USA, is an employee-owned high precision filtration and flow control company founded in 1959. The performance of filtration and flow control components is often an overlooked part of process optimisation, which can create inefficiencies later down the line. To improve process performance across healthcare, semiconductors, food & beverage, energy, and defence industries, Mott creates customised filtration and flow control solutions with tailored porosities.
Conventional fabrication techniques, such as axial and rolling compaction, can create reliable parts at a low production cost to help manufacturers achieve the aximum level of productivity. When manufacturers need efficient repeatability of components, traditional techniques are the most common and cost-effective option.
However, as applications call for more complex parts, these traditional fabrication techniques may not deliver the design flexibility required. Manufacturers may need to implement more complicated geometries to minimise pressure drop, increase filtration capacity, or offer some other functionality or performance benefit, which often cannot be created by using traditional compaction techniques.
Challenge
As Mott Corporation customers started to demand increasingly complex solutions and new application prototypes, it became apparent that traditional fabrication techniques did not enable rapid development cycles. Creating multiple iterations using these techniques can be expensive, because it requires multiple press and die tooling sets. If a customer wanted to change just one feature, they would need an entirely new set of tooling, which can slow the development process and dramatically increase costs.
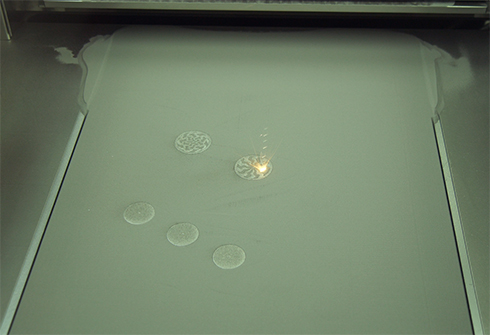
To address these opportunities and continue to provide solutions for its customers, Mott Corporation wanted to find a more efficient alternative to experiment with design and performance parameters. To provide its customers with additional solutions alongside the traditional pressed-sintered offering, Mott identified that additive manufacturing (AM) can deliver the design freedom and rapid prototyping capabilities needed during the development process. As it increased its understanding of the benefits of additive manufacturing to produce parts with porous filtration and flow control media, and enable new applications where traditional fabrication techniques were limited or impractical, Mott Corporation began looking at the best system for the application.
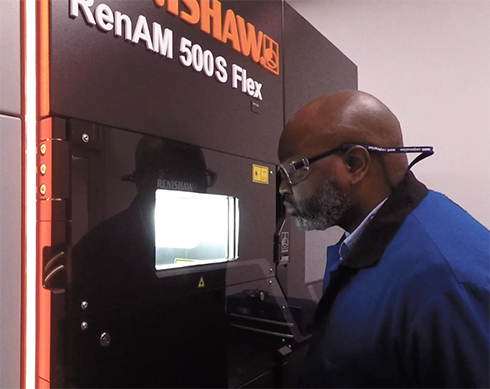
Solution
After deciding to invest in AM, Mott began working with a variety of providers to find the best system when developing porous components. While many of the companies in consideration had machines that could create the parts needed, Mott eventually approached Renishaw and invested in the RenAM 400. The system provides open architecture, enabling users to adjust multiple parameters, which is essential to research and development work. Soon after installing the machine, Mott Corporation was able to reproduce a range of porous media comparable to its conventional offerings. Some of the printed media exhibited performance improvements, such as lower pressure drop, compared to conventionally fabricated parts with equivalent geometries and pore sizes.
The company later upgraded to the RenAM 500S Flex system and benefited from improved filter life, more uniform gas delivery in the build chamber, better hardware, and laser control. The RenAM 500S Flex features the same optical, chamber and gas-flow design as the rest of the RenAM 500 series, but offers additional flexibility when changing powder. The Flex is configurable with one or four high power 500 W lasers that can be used in either modulated or continuous wave regimes, adding a further level of consolidation. Customers can also access every part of the powder system and easily switch between materials, which can be beneficial when developing parameters for a variety of alloys.
“When deciding on which AM provider to partner with, we contacted current users of the equipment to gauge their opinion,” explained Vincent Palumbo, Program Manager at Mott. “Renishaw had the best feedback, but also seemed genuinely excited and open minded about how we planned to use the technology. Renishaw’s customer service was therefore one of the selling points when working with the company, because the team provided us the support and flexibility required for our novel applications.”
Results
By installing the RenAM 500S Flex system, Mott Corporation has reduced machine turnaround and setup times by well over 50 per cent compared to the previous model, reducing the overall resource burden for each build. Additionally, the improved gas flow and re-coating mechanisms in the chamber have improved the standard deviation of performance metrics by approximately 30 per cent in certain cases. This allows Mott to have more confidence in the performance of the parts printed on this system.
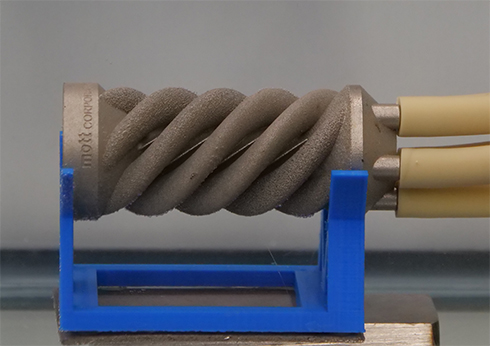
Renishaw’s unique degree of vertical integration in manufacturing and expertise in optical systems has enabled the design and manufacture of a particularly innovative optical platform. Renishaw was also able to further increase flexibility in its 500 series machines, with the capability to operate the laser in both modulated and continuous wave regimes. This broadens the scope of customising the process even further and allows users to increase manufacturing throughput without necessarily having to compromise quality.
“The Flex has been the most popular stop on our facility tours,” continued Palumbo. “It’s great to see customers’ reactions to the parts we have been able to create. It has also generated useful dialogue between us and our customers to come up with development projects, and think of other components we can design with them in the future.”
“The open architecture of the machine platforms provided by Renishaw has been key in enabling our development of these unique components. Renishaw has also delivered incredible customer support from start to finish. From support with technical issues to supplying consumables in a timely manner, Renishaw has been a reliable vendor for the past six years we have been working with them.”
For further information on the RenAM 500 Flex system, visit www.renishaw.com/am