Maximum speed thanks to optimum robot path planning and multi-pick function
Random bin picking with optical sensors is regarded as the ultimate discipline of automation. An enhanced version of ISRA’s proven bin picking sensor now enables especially good results and at a new top speed. This solution not only uses powerful four-camera technology and an embedded system architecture but also focuses on optimized robot path planning and a reliable multi-pick function. As a Touch & Automate system, the product is suitable for all major robot brands and can be deployed in production in a matter of hours.
The growing cost pressure and high-quality demands in the manufacturing industry require extremely efficient automation solutions. With its high degree of maturity, the PowerPICK3D sensor developed by ISRA VISION is the first choice for reliably recognizing parts – irrespective of their geometry or material. With an embedded PC, the smart sensor design does not require any extensive wiring to connect the camera and the PC. This accelerates data transmission and processing, in turn enabling extremely short scan times of less than 0.5 seconds.
For the complete detection of components, the sensor uses quad-camera technology in which four cameras scan the contents of the container from multiple perspectives. The multi-view images captured by the sensor thus enable reliable object detection for the precise generation of a point cloud – even when there are shadows and reflections on a component. By performing a comparison with the previously uploaded or scanned-in CAD model, the intelligent system then detects the components to be picked and automatically creates an optimized picking order and path plan. Moreover, the reliable calculation of collision-free robot paths enables fast and reliable operation with extremely short cycle times.
Reliable automation solution for every application
For the enhanced bin picking sensor PowerPICK3D, particular emphasis was placed on process stability and speed. As such, the sensor captures the entire bin after every scan through its continuous 3D container detection. A newly integrated multi-pick function into the sensor allows several parts to be picked reliably after just one scan by blocking areas where parts were previously moved. A practical solution has also been found for handling defective parts: If an unknown component is identified during scanning, the operator is notified by an alarm while production continues without the need for a cost-intensive shutdown.
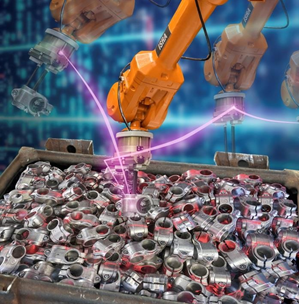
Automatic path planning: The highest level of process reliability thanks to collision-free planning
Additionally, downtimes can be avoided when it comes to material supply: Thanks to a modular and expandable multi-sensor layout, two sensors continuously scan two bins. As a result, just one robot is required for emptying two containers. Once the first container has been emptied, the second container can be worked on, so that production does not have to be interrupted unnecessarily. The decisive Bin Picking performance is further enhanced by the support of a complex gripping position. An optimal picking strategy and support for a seventh axis directly on the gripper make it easier to reach parts in corner positions. This maximizes the degree to which bins can be emptied. Altogether, the combination of new and enhanced features – with 60 cycles per minute – results in a new benchmark for bin picking.
The wide variety of sensors and the wealth of specialist expertise offered by ISRA VISION mean that there is a suitable solution for every area of application, which can also be adapted to complex systems and production lines flexibly and in line with customer wishes. The range of specialized sensors offers an outstanding “field of view” for component detection – regardless of the bin size or the position of the parts. All in all, the enhanced PowerPICK3D enables significantly higher throughput and faster cycle times than comparable sensor solutions.
Fast deployment with just one click
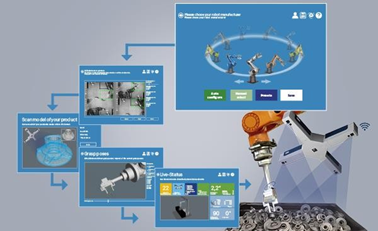
Moreover, the PowerPICK3D sensor solution is incredibly easy to install: The robot interface’s one-click setup guarantees a seamless connection to all major robot brands. The automatic calibration of sensors and robots also helps make the setup process quick and easy. A particularly innovative feature is its component detection, with a simple scan-based teach-in process for new parts.
Ready for connected production
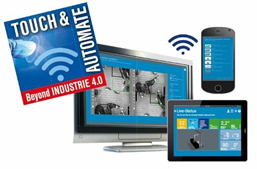
ISRA VISION’s bin picking solutions are presumably the most complete bin picking product portfolio on the market and are compatible with all major robot brands and standard communication interfaces. The sensors are standard- equipped with WLAN and remote access for every device and use the OPC UA communication protocol. With its intuitive application design and its range of digital networking capabilities, the portfolio is perfectly equipped for the future of industrial production in the smart factory.
To know more, please check ISRA Vision.