Delta, global leader in power management and a provider of IoT-based smart green solutions, is participating today in the Taipei International Industrial Automation Exhibition 2024 under the theme of “Charting the Path to Smart Green Manufacturing” to present its next-generation digital green factory solutions for low-carbon manufacturing. The showcase includes the new Virtual Machine Development Platform DIATwin empowered by AI algorithms and digital twin technology to save development time by up to 20% with high fidelity simulations, Smart Warehouse and Logistics Solutions that leverage 3D machine vision and a wireless charging system to optimize to optimize warehousing and logistics cost efficiency by up to 30%, and the new High-Speed Die Pick-and-Place Solution to enhance production yield as much as 20%.
Andy Liu, general manager of Delta’s Industrial Automation Business Group (IABG), remarked, “This is the crucial moment for factories to embrace smart green manufacturing in the face of global supply chain reshuffling, carbon pricing trends, soaring energy and production costs, and the worldwide AI boom. Delta not only integrates a new and broad industry-based smart manufacturing solutions, but also enhances data analytics by AI and implements cyber-physical integration in production lines to facilitate smart green transformation for cutting-edge high-precision manufacturing. Meanwhile, we continue to enable substantial energy savings for our customers, such as Delta’s AC motor drives, which helped save 1.676 billion kWh of electricity in 2023, equivalent to a reduction of 6.3 million tons of CO2 emissions.”
The Virtual Machine Development Platform DIATwin employs software to create virtual equipment for testing mechanical design and production plans, and to generate optimal recipe parameters by using AI. The solution saves equipment development time by 20% and offers full production life-cycle support, reducing costs and product time to market. In addition, Delta is demonstrating its innovative digital twin platform developed on the NVIDIA OmniverseTM platform. Delta’s digital twin platform can virtually link specific production lines and aggregate data from a diverse range of equipment and systems to generate synthetic data to train its computer models to achieve 90% accuracy. Delta has also invited NVIDIA experts to present at its booth how the OmniverseTM platform enables the development of applications such as DIATwin.
During Automation Taipei 2024 (from August 21 to 24), Delta is organizing booth tour sessions and seminars covering topics including various applications of the DIATwin and Omniverse, smart factories and machine networking, smart electronics assembly press-fi, SCADA system applications, factory green transformation, a smart injection molding machine solution, and more. Delta welcomes press and visitors from different fields to come to its booth (M420, 4F, Hall 1, Nangang Exhibition Center) to learn more about green smart manufacturing solutions.
2024 Automation Taipei-Delta Booth Highlights
Smart Warehouse and Logistics Soutions
Delta is presenting Smart Warehouse and Logistics Solutions, which provide a comprehensive integrated software-hardware system to efficiently increase throughput. Combined with Delta’s warehouse management system, the solutions reduce warehousing and logistics costs by 30% through workforce optimization and intelligent transformation. Highlights include: The High End IIoT Controller AX-5 Series that facilitates nanosecond computing speed and seamless integration with automated warehousing systems. Delta’s AC Motor Drivethat integrates power supply, relay and other peripherals for conveying and sorting equipment to reduce cabinet costs. The new 3D ToF Mini Camera DMV-TM that helps Automated Guided Vehicles (AGV) to acquire accurate depth data for efficiency and safety. The M∞Vair Series Wireless Charging Systems, ranging from 1kw to 30kw, that provides contactless power transmission to enable automatic contactless, wireless charging for AGVs, Autonomous Mobile Robots (AMR) and larger industrial vehicles such as forklifts and tractors for various industrial vehicles with a maximum of 95% end-to-end power transmission efficiency.
Smart Warehouse and Logistics Soutions
Delta’s High-Speed Die Pick-and-Place Solution integrates linear motors, optical linear encoders, and the Linear Pocket Actuator LPL Series, which is equipped with a force sensor to ensure high-speed, high-precision pick-and-place operations of dies (unpackaged wafer units). Aided by a compact low-voltage servo system, the solution enables soft die pick-and-place and gantry synchronization for excellent high-speed linear motion accuracy and stability. Compared to mechanism designs with ballscrews and pneumatic cylinders, Delta’s solution reduces cycle time by 15% while enhancing product yield by 20%.
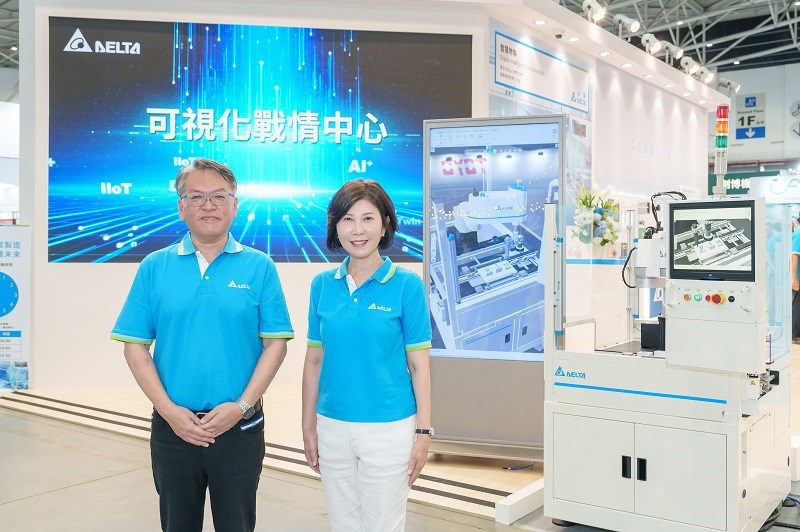