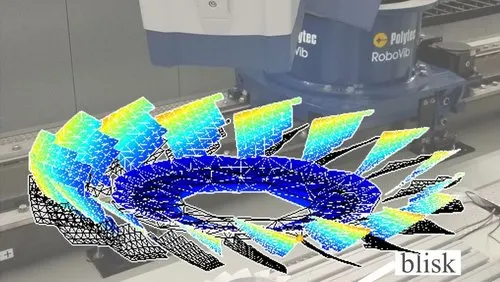
Blisks are milled from a single piece, unlike the conventional process of individually mounting separate rotor blades one by another onto a hub. Blisks reduce both weight and complexity but can bring up technical challenges. Since they are made from a single piece, they show extremely low damping values, whichcan cause pronounced resonances. Production-related asymmetries can lead to a strong concentration of vibrational stressand therefore component fatigue in individual turbine blades. Detailed finite element models (FEM) are the indispensable key for predicting stress on the blisk under operating conditions in an early development stage. These simulation results require validation and optimization by detailed experimental vibration measurement values.
The unique 3D scanning laser Doppler vibrometry (SLDV) from Polytec is an excellent optical method for capturing detailed measurement data from the blisk with highest accuracy. The modal parameters derived from the measurement data via PolyWave, the Polytec modal analysis software, enable a detailed correlation with the FE model. This helps to improve the FE model, which is essential for an accurate prediction of fatigue in later real operation. The entire process using SLDV contribute key insights and support the development of more efficient and safer engines.
For more information, visit https://www.polytec.com/int/vibrometry/areas-of-application/aerospace/turbines