If nothing else, a year of COVID-19 has taught us to expect the unexpected. Of course, manufacturers have always been highly attuned to change, but the COVID-19 pandemic hit the manufacturing industry seemingly overnight, causing deep and long-lasting impacts. A year later, we can look back and see what manufacturers have learned about how to adapt and succeed in the face of adversity.
At Universal Robots, we talk to thousands of successful, innovative manufacturers who are addressing the challenges of an uncertain world. Here are some of the proven approaches they’re taking, and that you can replicate.
AUTOMATION IS THE SINGLE MOST POWERFUL STRATEGY
The term VUCA refers to volatile, uncertain, complex, and ambiguous conditions—and it’s never been more fitting. For manufacturers, automation has emerged as the single most powerful strategy for succeeding in a VUCA world, whether that’s caused by a pandemic or almost any other business challenge.
For decades, automation has helped manufacturers improve continuity, flexibility, competitiveness, productivity, and employee safety. In today’s VUCA world, manufacturers are increasingly turning to collaborative automation. Flexible, intuitive collaborative automation is a natural fit when changes occur quickly, limiting time to plan, budget, hire and train employees for new skills, or undertake extensive plant and company reconfigurations.
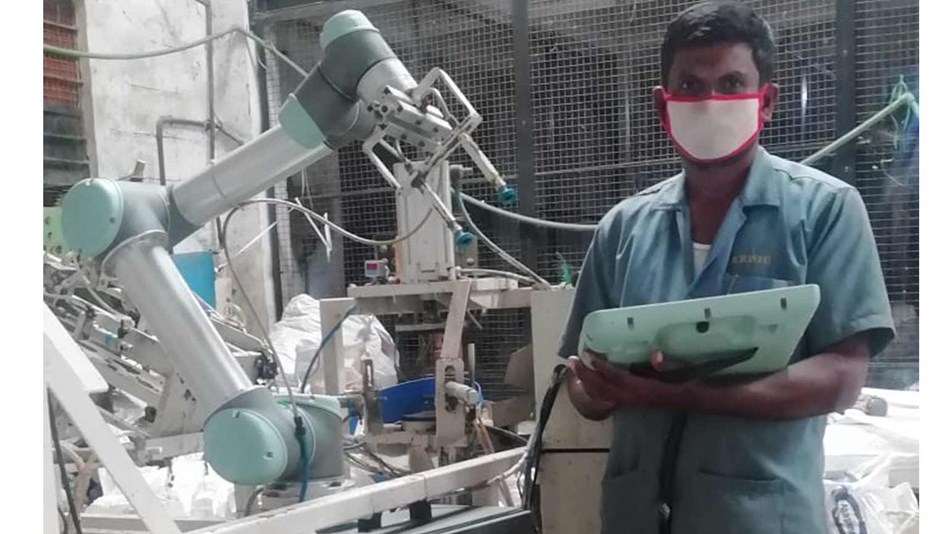
Irrigation equipment is critical for Indian agriculture and demand is high, but many firms have been hit hard by staff absences due to COVID-19. Krishi Group, one of India’s leading agricultural equipment manufacturers, was faced with a 40-50% reduction in its workforce, and struggled to keep up with demand until it introduced a UR cobot to its facility. The cobot now works alongside a human on quality control tasks that previously required two workers to complete.
SUPPLY CHAINS NEED A PLAN B
The global pandemic hit supply chains quickly and acutely, illustrating the vulnerability that had been building for years. Manufacturers now know that they need a Plan B in case remote production or supply is compromised and market demands shift. At the same time, many manufacturers have realized the advantage of being closer to their customers, even if that keeps them in regions with higher labor costs.
The key is to be able to manage workers in terms of their availability and safety, and to increase their value and skills to meet new production needs. Collaborative automation can help businesses of all sizes anticipate and respond more effectively to change—turning unexpected obstacles into new opportunities.
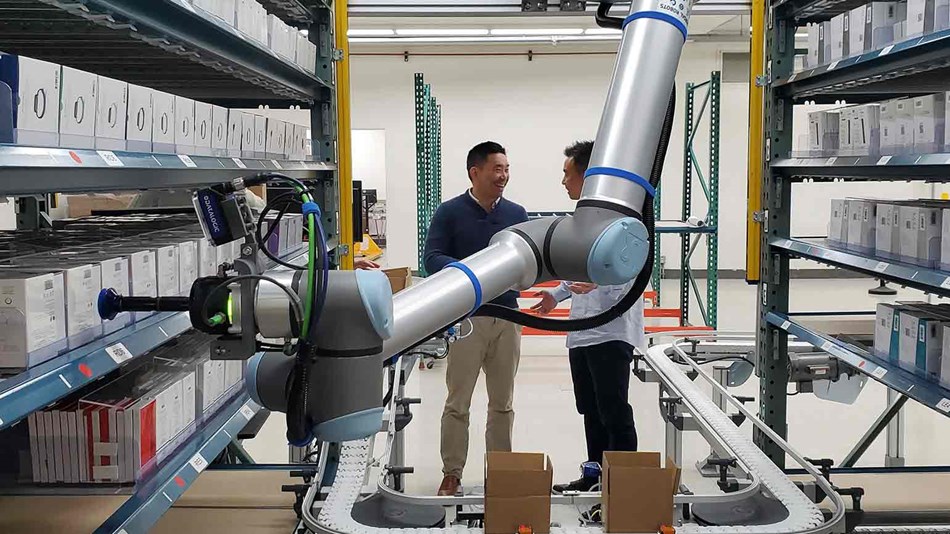
As the pandemic started spreading, DCL Logistics, a third-party logistics company headquartered in California, saw a 30 percent increase in business. Because of DCL’s new UR cobot powered systems and its ability to quickly reorganize labor resources, DCL was one of the only fulfillment centers able to handle the increase in orders without changing SLAs (Service Level Agreement) of “in by noon, ship the same day.” This turned out to be a major differentiator for the company during the pandemic with customers so thankful that they would send DCL employees catered lunches and gifts as a token of their appreciation.
LABOR SHORTAGES LEAD TO OPPORTUNITY
Previous off-shoring trends were fueled by lower-cost labor. Advances in collaborative automation, however, have drastically increased productivity and reduced costs across a number of manufacturing processes. Many of these can now be easily reshored and deployed domestically. While labor rates in traditionally low-cost countries have seen annual increases in the double digits, affordable collaborative robots make automation even more accessible, independent of company size.https://video.universal-robots.com/v.ihtml/player.html?token=14670591ffc0d1580e8f208eecd8df98&source=embed&photo%5fid=63686085
Revtech Systems, a Universal Robots CSI from Quebec, Canada, launched an internal challenge that saw groups of 3-4 employees join forces to design a face shield that could be produced in high quantities, fast. Once the final design was chosen, the team quickly set up a cell with a human operator and two UR10 cobots. producing an amazing 700+ face shields per day.
ADAPT TO MEET CHANGING DEMANDS
Uncertainty places increased demands on companies to turn on a dime. What if they suddenly have to produce something different than the plant was originally designed to produce? What if the market suddenly demands more customization?
Collaborative automation is designed to be easily learned and quickly deployed so that it can be moved, changed, and redeployed by in-house employees with minimal hand-holding.https://video.universal-robots.com/v.ihtml/player.html?token=f0a444e9b8e7cc73c0b976e9713f7f3c&source=embed&photo%5fid=63144966
Automotive manufacturer SEAT transformed an assembly line to the production of ventilators at its plant in Martorell, Spain. The UR10e was installed at the end of the line to do a quality check of the locking mechanism of the unit’s control box. The line was in operation three weeks in April 2020 and supplied 300 ventilators per day to ICUs in Spain.
MEET NEW SAFETY REQUIREMENTS
The importance of physical distancing during COVID-19 has made infection control a new priority, and for many manufacturers this new reality will continue indefinitely. Many successful manufacturers were able to reopen their doors more quickly with collaborative robots. By inserting UR cobots within standard production lines, these companies were able to offset face-to-face risks and create safe distance between workers while keeping output levels high.
LEARN MORE ABOUT NAVIGATING THE COVID LANDSCAPE
In many ways, we’re navigating uncharted territory, but a year into the COVID-19 pandemic, we’re finally seeing a promising future. Thanks to collaborative automation, manufacturers are discovering innovative new opportunities to address a VUCA world and emerge smarter, sharper, and better prepared for any situation.
Get more information on how manufacturers like you around the world are using collaborative automation to adapt and succeed.
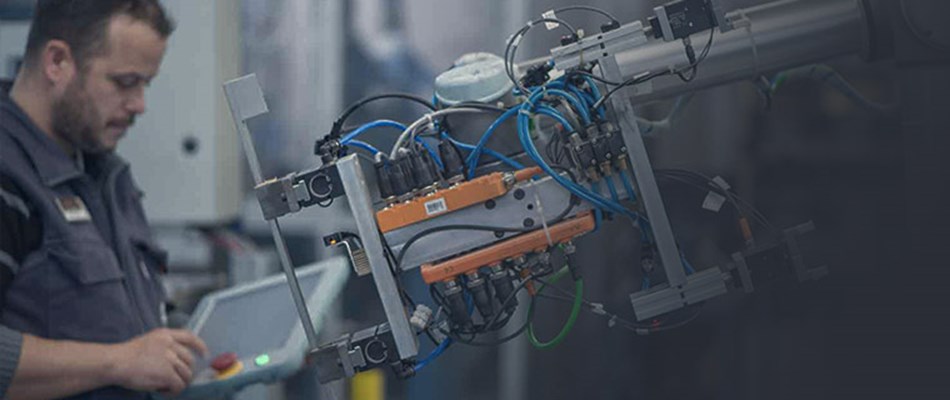
BEGIN YOUR JOURNEY TOWARDS COLLABORATIVE AUTOMATION.
Our whitepaper will arm you with the knowledge needed to do just that. You’ll learn what your current systems could be missing, and how to reduce risk and boost productivity.
UNIVERSAL ROBOTS
We believe that collaborative robotic technology can be used to benefit all aspects of task-based businesses – no matter what their size.
We believe that the latest collaborative robot technology should be available to all businesses. The nominal investment cost is quickly recovered as our robotic arms have an average payback period of just six months.