This is a white paper and has been reproduced in its original form.
Introduction
Visual inspection is the oldest method for quality control. The human eye has proved to be excellent at detecting cracks, deformities, scratches, missing components, and other errors and issues that can impact quality.
However, brands have a lot to lose if they mistakenly send poor quality products to the store shelf. In the food and beverage market, for example, the average cost of a product recall is $10 million. Possibly more damaging to a company’s bottom line, over 20 percent of consumers say they will not purchase from that brand again (Figure 1). A quick survey of current recalls from the US Food and Safety Inspection Service in November, 2021 showed that almost 30 percent of the 1,285 issued alerts were related to misbranding and mislabeling.
Manufacturers are under tremendous pressure to ensure end-to-end quality for their products, especially as consumers increasingly demand perfection. And a great deal of that pressure still falls on human visual inspection.
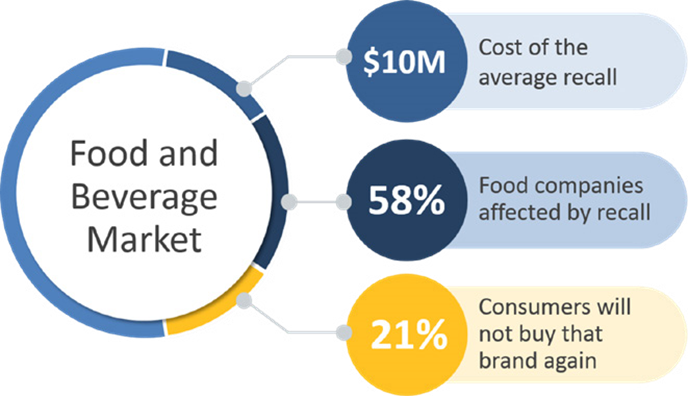
Humans versus Machines
Every few days, there’s a new headline warning that artificial intelligence (AI) is poised to take away jobs from humans. Undoubtedly, there are tasks where machines are more cost-effective and efficient than humans. Buttons replaced the elevator operator, and machine visionpowered robotics has significantly changed large scale manufacturing by taking on many dull, dirty, and dangerous tasks.
For quality inspection, it’s not quite that simple. Machine vision brings speed, accuracy and repeatability that we simply can’t match as humans. However, many of the advances in automation technologies, including traditional computer vision and more advanced machine learning and deep learning, really aim to replicate what we do very well as humans.
We excel at sensing differences through sight, touch, and even smell depending on the product. We can distinguish subtle flaws, variations or differences and can adjust when faced with unpredictability. Humans are also easily trained. We learn by example and can adapt for new products or requirements.
Despite these human advantages, we also suffer from a number of limitations. Our eyes can be easily tricked, making us unreliable. Try and count the black dots in Figure 2. A machine vision system make decisions faster, thanks to higher processing speeds and ever-expanding memory capacity. Automation can be programmed to be unbiased and consistently accurate.
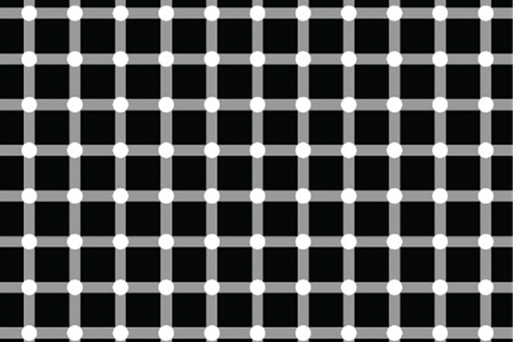
Unlike machines, we get tired, bored, and distracted. As a result, most manual inspection tasks typically exhibit error rates of 20-30 percent, primarily due to human error. Typically, these errors are related to missing a defect, incorrect assembly, or a “false positive” where an operator identifies an issue that does not exist.
Considering these error rates, and the resulting higher costs due to waste and manufacturing downtime as well as potential brand risk, there’s an obvious opportunity to leverage technology advances to help human inspectors.
AI-Powered Decision Support
Adding automated decision-support to visual inspection helps speed inspection rates, improve end-to-end product quality, and provides more qualitative product evaluation to ensure manufacturing processes are repeatable and traceable. As consumers increasingly demand more customized products, human inspection can sometimes be more cost-effective and adaptive than automated processes for on-demand and low volume manufacturing. New visual inspection systems leveraging advances in no-code algorithm development and edge processing platforms make it easier and more cost-effective for progress and finished goods. These systems provide pre-packaged inspection skills that can be easily customized and retrained for specific requirements, including verifying components, inspecting labelling, checking assembly, and digitizing work instructions.
As consumers increasingly demand more customized products, human inspection can sometimes be more cost-effective and adaptive than automated processes for on-demand and low volume manufacturing.
As a fully integrated tabletop system, the operator can use the camera, edge processing, and display to acquire images and create an AI model. They don’t need to switch between cameras, PCs or cloud-based systems; making the system easy-to-use, highly cost-effective, and all in a smaller footprint.
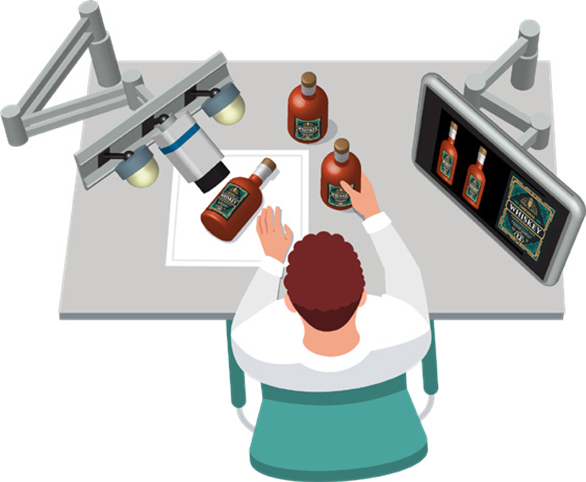
No Code Advantages and Simple Training
One of the most significant hurdles for manufacturers considering AI-based inspection is algorithm development. There is a perception that it requires specialized skills, or expensive consulting, to deploy the technology for manufacturing applications.
No code block-based platforms let any end-user easily design AI and computer models to automate tasks, such as visual inspection, digital work instructions, automated counting, and measurement.
For visual inspection systems, pre-packaged skills for common requirements such as image compare and image save can be quickly trained and deployed, without requiring programming language expertise. With just one good image (a “golden master”) the system is trained to distinguish good from bad. More experienced developers can use the software platform to customize pre-packaged skills, or open source machine vision and AI code, for unique requirements.
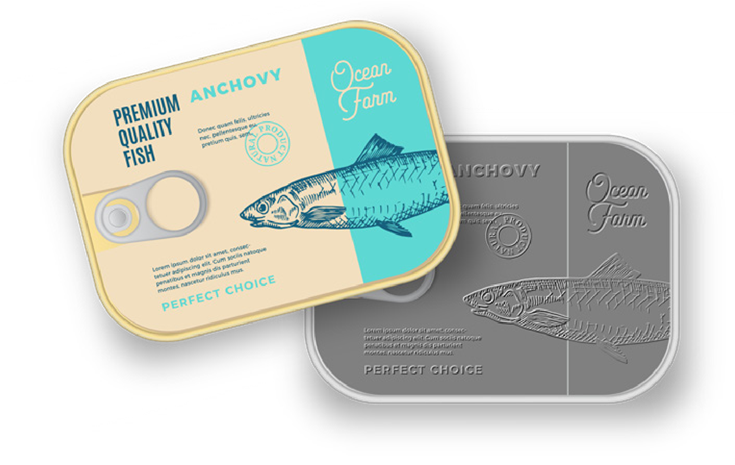
Augmented Reality and Image Compare
One of the fastest ways manufacturers can add AI decision-support into processes is with camera-based augmented reality. Augmented reality provides a real-time view of a product on a display, with computer generated graphics to help guide an operator. For a manual assembly process, the system provides real-time visual feedback to verify results.
In one example, a distillery is using augmented reality in its labelling process. The company operates in a highly competitive market, and its unique bottle and labelling is a key differentiator as a consumer scans a crowded store shelf.
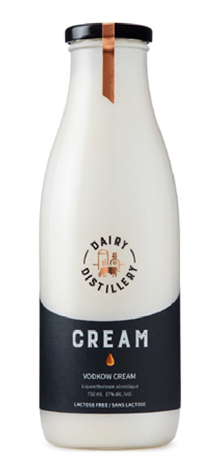
In this application, an automated system places the main label on the bottle. It’s then up to a human operator to accurately place a smaller, transparent label that aligns with corresponding visual brand elements on the main label. With a few different products, fast-changing production schedules, and varying packaging requirements, it’s uneconomical to automate this secondary labelling.
The visual inspection system stores a “golden master” image for what each product should look like when it reaches the store shelf. The operator places the bottle under the camera-based system, and a “golden master” overlay guides their placement of the secondary label. The system is tuned with thresholds to accept a margin of error, but to the human eye the labels all appear perfectly aligned.
The systems adds a few extra seconds to the overall manufacturing process, but saves the company time and cost if labels have to be removed and realigned. It also helps speed training for new operators, and removes human subjectivity from the process. If the manufacturer changes the bottle or labelling, with “no code” algorithm development an operator or quality manager can easily redesign and train their own AI model and deploy it to edge processing integrated in the system.
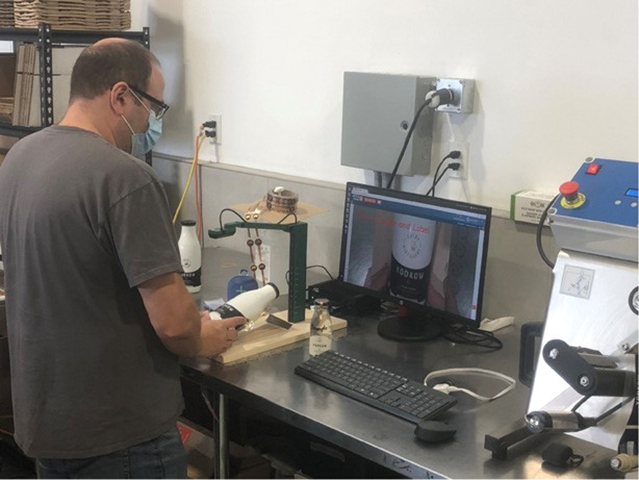
For the distillery, the visual inspection system offers many valuable benefits:
- Reduces subjective decision-making for the human operator, especially over a long shift, where the system is consistent and accurate.
- Cost-savings, as labeling does not have to be removed and reapplied if an error is detected during the final phase of production.
- The system is quickly trained with images of “good product” for multiple product lines. An operator or quality manager can train the system, with no programming skills required.
- It’s faster to train new employees on understanding the relationship of key elements of the brand.
Similarly, image compare capabilities are used to match the approved layout and final production for electronic assemblies. The system quickly compares the placement of components on the circuit board, and highlights differences and deviations for the human inspection before it moves to the next step in the manufacturing process or to final packaging.
In addition, the manufacturer use the system to capture and save an image of every printed circuit board. This data is shared with traceability systems for inventory and shipment management and batch tracking, as well as other business processes including root cause analysis for defects.
Changing Visual Inspection
Adding decision support and automating processes for visual inspection helps ensure consistency. The technology can aid a tired operator at the end of a shift, a new employee who is unsure what makes a product “good” or “bad”, or simply speed the inspection process. It lets manufacturers take advantage of new technologies for processes where automation is cost prohibitive, including low volume production.
As part of a wider Industry 4.0 initiative, automation and decisionsupport tools for visual inspection can help provide real-time process visibility to drive data-based decisions.
To learn more about Pleora’s AI Solutions visit pleora.com/ai-for-quality-inspection/