CASE STUDY:
ATI Casting Service is an iron casting foundry and full-service machine shop that specializes in making large castings utilized in wind energy and other markets. Previously, ATI used a combination of a fixed CMM, a laser calibration system and an interferometer to measure their wind turbine hubs. This assortment of devices was slow and complicated to use.
ATI decided to implement a FaroArm® and FARO® Laser Tracker, which resulted in dramatic time and money savings, in turn creating new business opportunities through higher productivity.
The US Department of Energy has set a goal of obtaining at least five percent of US electricity needs from wind power by the year 2020. This means that the demand for “green energy” such as wind power is growing. One company that has taken full advantage of wind power’s exploding growth is ATI Casting Service in Alpena, Michigan. As a member of the AWEA (American Wind Energy Association), ATI Casting Service (www.aticastingservice.com) has been involved in the wind industry for over 15 years.

“Wind energy is environmentally friendly and the price of wind is not going to change, it’s always free – unlike coal, natural gas, or nuclear fuels,” said ATI Casting Service President David Neil. “This fact and with the DOE’s 2020 goal has resulted in a rush to produce wind turbines to get onto towers to start producing energy. Our customer base has grown as well as the demand of our existing customers.”
ATI Casting Service is an iron casting foundry and full service machine shop that specializes in making large castings utilized in wind energy and other markets. They produce turbine hubs, gear-box castings, and other components for wind turbines. Their high quality ferrous castings are manufactured with the latest in scientific technology and modern manufacturing methods. Problem.
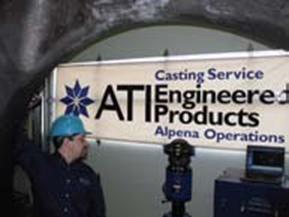
In their manufacturing processes, ATI Casting Service must measure the castings they make for wind turbine hubs. These hubs are for the wind mill’s long blades. Depending on the size of the turbine, each wind mill can consist of between 10 and 20 tons of iron castings with each individual casting ranging in size from less than 200 pounds to over 50,000 pounds. The hubs alone for commercial wind mills can easily weigh as much as 36,000 pounds and be large enough for a grown man to walk through. With such staggering numbers, ATI Casting Service is one of the few metal casting facilities with the capability of pouring such large components.
It takes several steps to create such large castings. The hub is started using a silica sand mold, is cast with molten iron metal, and later cooled to shape. Once the hub is formed, it is extracted from the mold and cleaned with a shot blast machine. After going through numerous other processes, the new hub is finally inspected for exact customer specification.
Previously, ATI Casting Service used a combination of a fixed CMM, a laser calibration system, and an interferometer to measure their wind turbine hubs, which are often approximately eight feet in diameter. This assortment of devices was complicated to use, was not very fast, and did not offer the reporting that is so often required today. In addition, the fixed CMM could not read the various sizes of parts that ATI Casting Service needed to measure.
Solution
ATI Casting Service wanted a solution that was easy to use and provided the reporting they were previously lacking. Of course, being able to capture the information they needed was important too. They gained all of these by choosing to implement a FaroArm and FARO Laser Tracker. Both are portable CMMs that offer the speed and the reporting that ATI Casting Service required.
Based on the size and scope of the individual hub, ATI Casting Service uses the FaroArm, the Tracker, or both to perform the necessary measurements. The FaroArm is placed inside the hub so data can be collected on the inside dimensions. This is perfect for all of ATI’s castings where diameters are within the FaroArm’s 12-foot working volume. The Laser Tracker, with its working volume of 230-feet, is ideal for even the largest of hub dimensions. With either the hard probe of the FaroArm or the SMR (spherically mounted retroreflector) of the Tracker, ATI Casting Service can trace the outside of the hub to verify the dimensions of the drilled hole-like patterns as well as the flatness of the surface.

Implementation into the ATI Casting Service process was easy and the technology was quickly accepted by everyone – due mostly to the fact that both devices are easy to use and to understand. In less than two weeks they had completed training and learned practical applications.
ATI Casting Service uses both the FaroArm and the Laser Tracker to measure their parts and for machine alignment. The devices are used in their hub qualification process and for certification of alignments. They even gained the ability to level very large machines in-house. ATI Casting Service is now able to produce read-out reports of completed work for verification and for customer review.
Return on Investment
For ATI Casting Service, the greatest value has been in the time and money savings they have gained. Before, they would have to use an outside contractor for their machine qualifications. That cost thousands of dollars for two days of service. Now they do that same service with their own personnel and in half the time.