Additive Manufacturing (AM), or 3D printing as it’s known by many, is a technology that has been around for a number of decades. Over the past few years, it has come to prominence with more manufacturing technology providers venturing into the world of AM machinery. Deputy Editor, Tom Lane, takes a look at how this technology is changing the way manufacturers think about production.
There are many uses for AM technology which undoubtedly aid the manufacturing process. The advantages of rapid prototyping to speed up the design process and the many lightweight AM materials that can be used, as well as the ability to reimagine how a product, part or process can be refined for a specific purpose, all contribute to the benefits. However, the uptake of using AM has been limited for general manufacturing purposes for a myriad of reasons. Cost of materials vs mass production being one of the main bugbears I have heard time and time again as to why we do not see more AM based products on the market.
When talking about this technology its advantages are clear, but cost and speed of production have put limitations on industries venturing into the world of AM in a big way. The major players in medical, motorsport and aerospace have been successfully using this technology for some time to produce ground-breaking designs. You will not see a major motorsport or aerospace company garage without a 3D printer or two to hand, to quickly manufacture vital spare parts that keep their vehicles and planes moving.
Like many technologies looking to break into the mainstream of production, it often takes a disruptive force to intervene. And as much as I am tired of writing these words, the COVID-19 pandemic has been that force.
Reacting to a problem
The pandemic has resulted in a lot of innovation and adoption of new technologies, which we have covered countless times in these pages. However, the medical breakthroughs that have come as a direct result of COVID-19 have been a wonder to behold.
One such example has been the new 3D printed COVID-19 testing swab which can collect sufficient viral material from the back of the nose without need of a throat swab, now being manufactured in Scotland.
The Nasopharynx 3D printed swabs provide a less intrusive experience compared to traditional cotton bud swabs, cutting testing time, reducing anxiety and minimising discomfort for patients.
The Medical Device Manufacturing Centre (MDMC), based at Heriot-Watt University, and the Scottish Manufacturing Advisory Service (SMAS) at Scottish Enterprise, have worked with Scottish company Abergower to help manufacture the new design.
The unique helix designed tip of the swab and its tiny features guarantee that sufficient material is collected to provide a definitive result. The unique configuration of the tip of the swab allows capillary retention of the liquid as well as preventing the liquid from escaping the tip. The amount of viral load is further increased because the swab is non-absorbent unlike most cotton varieties.
“We are very scalable – that’s one big advantage about 3D, the fact that once you’ve got the process defined and the matrix of your production, quality control and sterilisation times, it’s just a question of scaling it by increasing the number of systems running our process.” Robin Prior MD, Abergower
Scaling production I spoke with Robin Prior, Managing Director of Abergower, who has the exclusive license to manufacturer the swab to find out more. “We have produced a work schedule that we can scale from, moving from 100,000 to 500,000 a month fairly quickly. It just depends on getting the orders,” Robin said.
“We are very scalable – that’s one big advantage about 3D, the fact that once you’ve got the process defined and the matrix of your production, quality control and sterilisation times, it’s just a question of scaling it by increasing the number of systems running our process.”
Professor Marc Desmulliez from Heriot-Watt University, Manager of the Medical Device Manufacturing Centre (MDMC) who helped get the project off the ground, explained why AM worked so perfectly in this instance over other manufacturing technologies.
Marc said: “Additive manufacturing as a mass production facility is very unusual. The rationale behind using AM was that the feature – the tip of the swabs – have a microfluidics property which will be quite complex to replicate using injection moulding. I am not saying it cannot be done, it can be and there has been some recent examples in Singapore where people have been, let’s call it ‘mimicking’ what has been happening. But it would require the substantial expertise in engineering to make the mould.
“With AM, you could manufacture say 400 swabs within half an hour without a problem at all. So that was quite an unusual experience for me as my first reaction as an engineer was to say, why would you want to use additive manufacturing to do mass production? It does not make any sense. But there was some very compelling evidence so that was the right way forward.”
Cost implications are still one of the biggest barriers to adoption of this technology, however the accuracy, unique design and the quality of the product really lends itself to the medical sector, as Robin elaborated: “It is more expensive than the common product, but it delivers so many more advantages because of what it can do. The whole idea of testing is getting accuracy and we think we can really significantly enhance the accuracy with our products much more effectively than a cheap swab.”
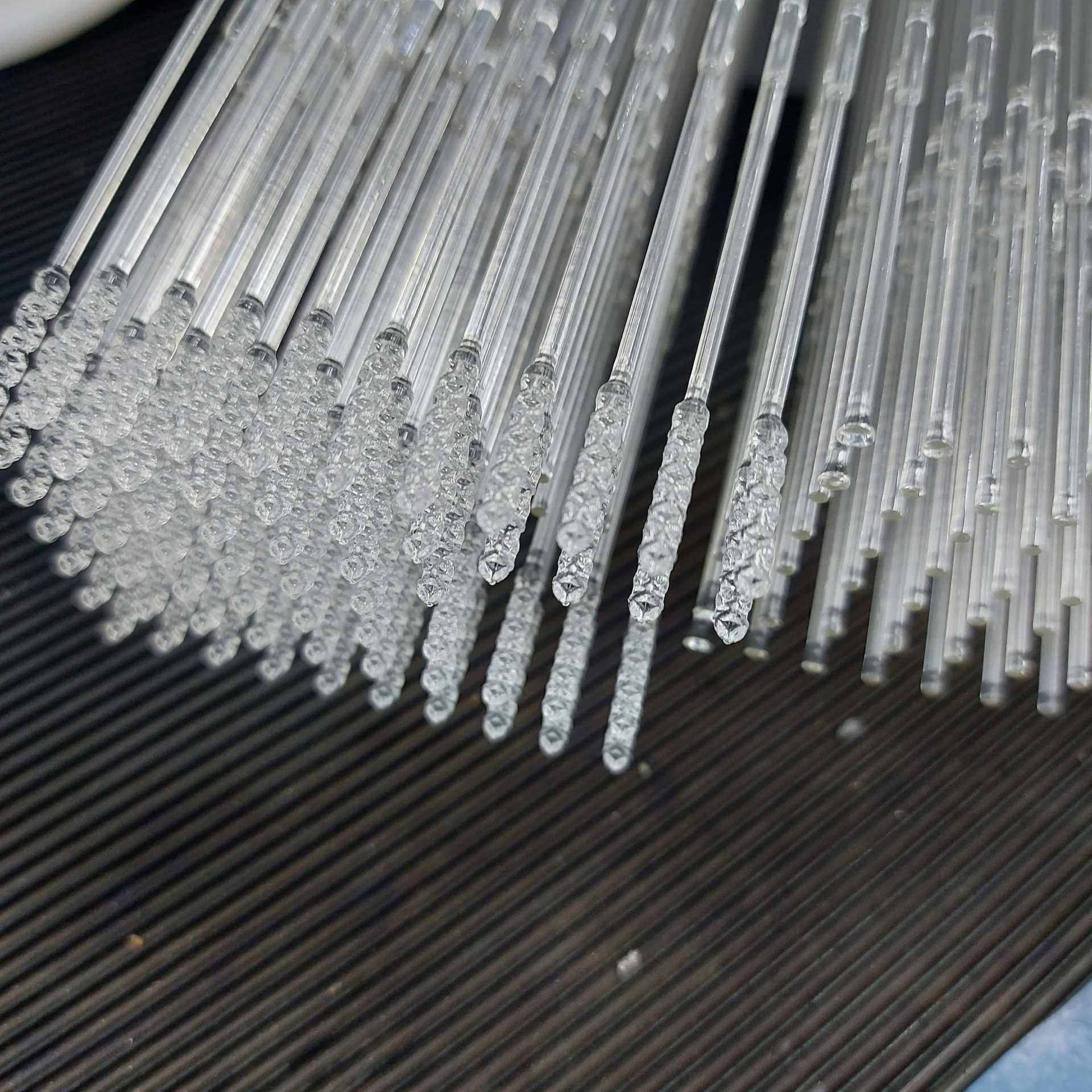
Function and dynamics
One of the key aspects of AM is the dynamic approach to production that can be taken. Engineers can reimagine the design process around the function of the product rather than the limitations of the technology they’re using.
Jerome Finlayson, lead practitioner at SMAS, pointed out that these production methods have really helped in the battle against the pandemic: “With COVID-19, everything was developing very quickly, you really needed the dynamic approach to tackle it. 3D printing lends itself to being dynamic because you’re just changing a software file, that break point is quite a critical piece.”
He continued: “When we looked at the number of vials being used in COVID-19 by the UK government, there were over 50 different types. So, then you start thinking, if we are going to be supplying all of this, you really need flexibility. If you had the injection moulding, you would have to buy new tooling. The timeline was too quick for the injection moulding capacity we have in Scotland; by the time they got the tooling made, it would be too late. So I did not get the impression from speaking to injection moulders that doing 3D printed swabs was probably going to be a business benefit for them.”
Thinking outside the box
AM still is not a widely used technology, but what we might be saying in 5-10 years’ time is that the pandemic changed the perception of how technology can be used. The advantages of rapid prototyping have been the main USP pontificated by the technology providers, rather than its mass production capabilities. But within this story we see how the scalability, accuracy and a bit of tenacity can really shift perception of the technology into a mainstream form of manufacturing.
Jerome concluded: “I think the real light bulb here in this story is that Abergower was not using AM as most companies would use it, for rapid prototyping of low volume, high complexity products, which is the traditional way of using AM.
“Its model contained some complexity in the swab head, but the product is essentially a low complexity, high volume product. And the beauty here is that the provider of the 3D printing technology that Abergower used understood the concept. We now have the model that can be scaled, so if you did the maths you could produce 400-800 swabs an hour per machine. And what we could then help Abergower with was – well, how many machines do you need to produce 200,000 a week because that’s what NHS Scotland needs.”